I felt i needed to consult others before attempting one of the bigger jobs i have to do on my truck and one which is preventing me from insulating and cladding the roof & generally slowing the project down. That is, how to go about constructing skylights.
I have a fibreglass roof supported by steel & aluminium supports that are glassed in with the rest of the roof. These supports are spaced about 2ft apart. My initial plan was to have two large skylights (one above lounge & kitchen area) by cutting through one support per a skylight & bracing to the other supports with steel strips and roofing bolts (as no welding experience as of yet)! However i have been warned away from doing this by a few individuals who say this will drastically affect the strength of the roof, and as im a total newbie to messing around with things of this nature to just stick with putting in skylights between the steel supports.
Ive had lots of head scratching about how to construct & fix the skylights securely (i hadnt so much as picked up drill before this project but have now learnt to build doors, worktops, a table and cabinets etc). Im really stubborn about not settling for horrible caravan/motorhome windows but not sure how i can achieve a weatherproof solid opening skylight. From studying other skylights it seems i need to build a kerb/frame that is fixed to the roof permanently and an opposing frame glazed with polycarbonate sheet that is fixed and sits on top.
- Sould i construct the frames from wood or from aluminium 'L' section (bareing in mind i 'currently' have no welding or metal work experince). I was told by one individual if i use wood for the frames, its gonna leak!!! Is this true? I feel more comfortable working with this material. Would a kerb frame from 'L' section with an opposing wood glazed frame be the way to go?
- How should i secure the kerb frame to the roof (Adhesive/screwed from underneath etc). As regards the two frames, do i just build two rectangle/square frames with the glazed frame slightly bigger so it slots right over the kerb or maybe router a rebate so the frames sandwich together?
- I have a gut feeling these skylights can not just sit on fibre glass and will have to supported (or maybe im wrong?), how can i do this?
I guess what im really after is a detailed walk through guide on building and fitting DIY skylights that look the job and dont leak from anyone who's pulled it off before.

I am particularly interested in how you Sharkey did the skylights in your Chevrolet C-40 as from the photos the two big skylights you have is exactly what im after. Did you construct and fit these yourself or buy and fit commercially made rooflights??
There are some pics of the roof of the truck to get an idea of what im trying to do. Plus just one of the truck so you guys can see the ol' girl!

Any help and advice is moochus appreciated
Thanks. Dan
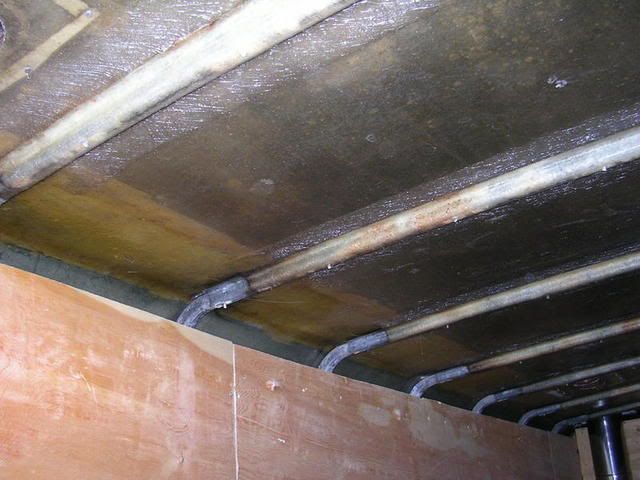
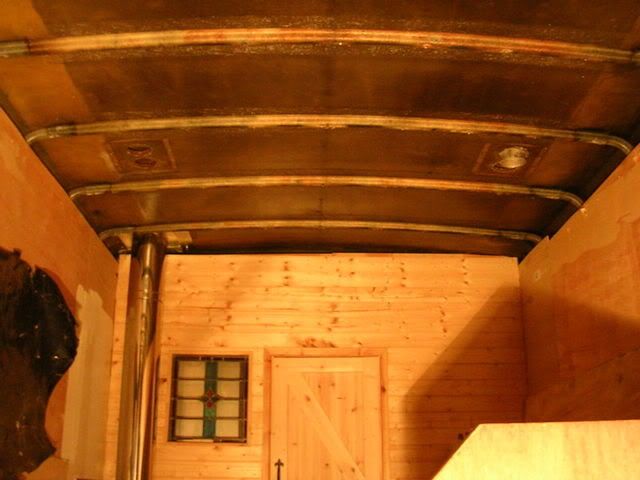
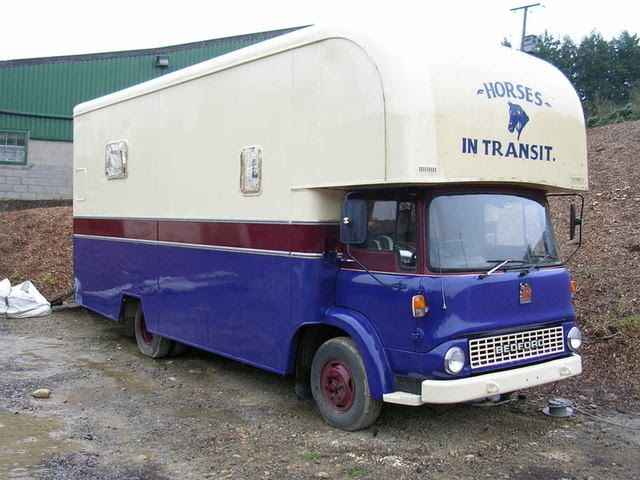